Stand Build Rules & Regulations
Air Conditioning & Ventilation
The CE marking (formerly the EC mark) is a mandatory conformity for all equipment installed at the event (video walls, computers, tablets, etc.). This mark is a minimum requirement, with part of the certification process to reduce likelihood of disruptive radio frequency interferences. This standard does not however guarantee that a given piece of equipment will not cause harmful interferences; this remains the responsibility of the exhibitor. In dense environments, such as an event, even minor issues can have a disproportionately large effect. For prototype equipment or demonstrations that require the use of licensed spectrum, please refer to the Wireless Policy: Cellular Frequencies.
All exhibitors who intend to install a video wall larger than ten square meters must send the make and model details, and relevant CE certification, to the following email address: mwcbarcelona.internet@firabarcelona.com. Exhibitors must specify if the video wall will be used permanently or occasionally during the Event. Certifications should also be provided for the equipment that is used to drive the main screen (Video Matrix, controllers etc.), as these can also emit signals that can cause interference.
The Organisers or its designated representatives may check that video wall installations have the relevant CE marking, as well as if the equipment is radiating across in any protected, licensed or requested band, causing detrimental interference to others. In all cases the exhibitor will be required to take immediate action to rectify.
Recommendations to reduce interference:
- Use of superior quality cables and wiring/installation methods
- The shielding of cables and power sources of any equipment that may cause interference to communication services, such a power sources of video walls, computers, etc.
- Non-modification of any electrical equipment as this can lead to generation of interference and invalidate the CE certification
The Organiser reserves the right to measure and evaluate signal emissions from any equipment and if found to be causing interference, even if carrying a CE mark, will require immediate rectification or the shutdown of the source of interference
Hall | Maximum Build Height |
Hall 8.0 | 5m |
Hall 8.1 | 5m |
Technical trusses for lighting or suspending structures are allowed up to 5.70m, ground level to top of truss. Although this is possible in most areas, there are some locations where these heights may not be available. Please check this with the official rigging supplier when you order your rigging points. Branding, logos or banners are not allowed above 5m. Black or white unbranded fabric, stretched across the technical truss in order to improve the visual aspect from above, is allowed. Please note that the technical floorplans do not consider the permitted height of trusses. All rigging heights must be checked with the official rigging supplier.
Exhibits which are taller than the permitted height limit such as antennae, may be acceptable. Please contact Abraxys for such requests
Double Deck / Two Storey Stands
- Any spaces with a permissible build height of 5m or over are permitted to build a double deck stand
- Structural approval of double deck stands, and other complex structures, have an associated cost. All costs for obtaining certification are at the cost of the Exhibitor
- Exhibitors with double deck stands must also complete the Double Deck Health & Safety form in order to highlight their planned control measures to prevent accidents when working at height
- The Organisers, the Venue and their approved Structural Technicians reserve the right to request structural calculations and approvals at the expense of the Exhibitor, pre-show or on-site, for any stand or structure at the Event
- Exhibitors must ensure that their stand designers make allowance for a comfortable head height clearance on each floor, taking any hanging or rigged elements into consideration
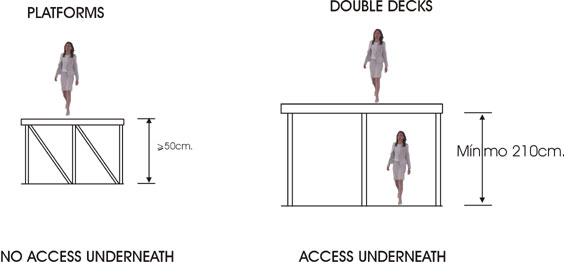
Please note:
- Rules relating to the build of double deck structures within the confines of the venue, are rigorous and venue specific. All construction is subject to the rules and regulations of the Spanish CTE (Código Técnico de la Edificación). Please click here to view the Spanish CTE (Código Técnico de la Edificación)
- All complex structure, outdoor structures and complex suspended structures must receive a formal certificate of stability from Graó Tècnic, the official Structural Technicians for the Venue. This certificate has a related cost which will be communicated to the exhibitor by servifira
- The above descriptions are a guide only and due to the nature of the regulations cannot be comprehensive. It is the decision of the venue, structural engineers and Abraxys Ltd as to whether the stand must be deemed complex. Their decision is guided by global exhibitions regulations and local law
- Exhibitors who wish to upgrade to a double deck stand should contact their appointed Account Manager
Ceilings and roof installations that can be seen from an elevated position; in particular from the Upper Walkway, and the venue escalators, must be finished to the same standard as the rest of the stand.
All space only stands must at least be ‘capped off’, where the top of stand is dressed to conceal internal structure when viewed from above.
The Organisers may, at their discretion, require changes to be made to ceiling and roof finishing, at the additional expense of the Exhibitor.
Where any door or gate is at the head or foot of stairs a landing shall be provided between the door or gate and the top or bottom step. The depth of the landing shall not be less than the width of a flight of stairs. Doors should always open away from the stairs.
Manual sliding doors are only permitted in rooms with a maximum capacity of fifty (50) persons
Automatic sliding doors are only permitted with backup security systems that automatically open the door in case of a power cut and a manual override button that can open the door in case of an emergency. Such installations must be made with a 24h power supply
Sliding doors that are in emergency routes also h be fitted with above mentioned security systems for automatic sliding doors
- For more technical details of electrical installations please click here to read the Electrical Safety section.
- Venue the power is supplied through service chests. Please note that each service chest supplies up to 63 amp (3 phase). For power higher than 63A, a special connection will be required and quoted separately.
- All service chests must be always accessible. Platforms must leave access to the service chest underneath.
- Connections until 63A will be carried out through a CEE form of an appropriate intensity (16, 32 and 63A, three - phase)
CABLES:
- The type of cable used between the venue supply box and the stand switchboard shall be 0.6/1 kV isolation type. Conductors to be used in the stand installation must be 0.6/1kV isolation level. Conductors of 450/750 V isolation level can be used with a rubber isolation (Type H07RN-F)
- Colour code to identify the phase conductors is black, brown or grey. Blue is identified for neutral conductor and the green / yellow for ground conductor
- Minimum section of the conductors depends on the protection installed
MCCB (Amperes) |
Minimum section (mm) |
6 |
1.5 |
10 |
1.5 |
16 |
2.5 |
20 |
4 |
25 |
6 |
32 |
6 |
40 |
10 |
50 |
10 |
63 |
16 |
80 |
25 |
100 |
35 |
125 |
50 (35 for open air conductor) |
160 |
70 (50 for open air conductor) |
- The ground conductor must be of the same section as the phase – neutral conductors until 16 mm2. From 16 mm2 on, it can be reduced by half
- Metal structures, receptors and, in general, everything that has metal parts and that could become live if a fault occurred, shall be connected to the ground distribution
- Trusses must be earthed, if any electrical installation (light fitting, wall outlet, cable etc.) is present in its immediate vicinity (on/below/through the truss)
- Aluminium system stands must be earthed
- Steel constructions must be earthed, if any electrical installation (light fitting, wall outlet, cable etc.) is present in its immediate vicinity (on/below/through the construction)
- Earthing takes place by a separate wire, connected as close as possible to or at the earthing point of the switch and distribution box (depending on the situation, by means of “plug in wall outlet” (if a better solution is not available)
- Junctions can be made with wire connectors, provided these are suitable for the (flexible) cable in question
- Junctions (whether within arm’s reach or not) must be protected by a junction box
- Earth leakage circuit breakers must have classification A (AC are not permitted)
- Splitters are not permitted
- All lighting circuits and outlets of less than 32A shall be protected with 30 mA residual current circuit breaker (RCCB). All electrical equipment that is accessible to the public must be also protected with 30 mA RCCB
- All circuits must be protected against overcurrents with omnipolar cut off (phase-neutral) in its origin
LEGAL RESPONSIBILITIES:
- Only Spanish regulations will be accepted. For any other case not explained, please follow the current Regulation of Low Voltage (Reglamento Electrotécnico de Baja Tensión) published in the Royal Decree 842/2002 (Real Decreto 842/2002)
- Power distribution within a stand must be legalized by a single and unique owner. Legalizations are made stand by stand
- Installations must be standardized and certified by a licensed electrical installer authorized by the Autonomous Catalan Government (Generalitat de Catalunya) who draws up the necessary documentation
- Stands up to 50 kW require a Technical Design Project
- Stands with more than 50 kW power must be legalized through an electrical project conducted by a local collegiate engineer. This electrical project has a fee. For more information, please contact servifira
- The power supply will be available from 07.00 to 23.00 during the exhibition period, except on the last event day, when for logistical reasons power to stands in exhibition halls will be switched off at 18.00. Exhibitors who need power at any other times (including dismantling) must order additional power. The additional power will be installed on a different switchboard e.g., if 24-hour power is required there will be two different switchboards
- All Space Only stands will be supplied with the following power supplies depending on the size of the stand space. If more power is required please contact servifira in advance
Stands up to 18m2 | Stands above 18m2 |
1x 3.3kw/16A Switchboard | 1x 6.6kw/32A Switchboard |
3x Embedded Sockets | 3x Embedded Sockets |
Enclosed Exhibition Stands (50% Rule)
NOTE FOR BUILD-UP: Visual enclosures to protect privacy during build-up are only permitted if they are structurally sound and are kept within the boundaries of the stand space. |
Untreated wallpaper and similar thin surface finishes, not exceeding 1mm in thickness, may be accepted, provided they are fixed firmly with an approved adhesive.
Artificial silk flowers are acceptable providing they have been fireproofed and are marked as such or are accompanied with supporting documentation.
- British Standards: BS 5438 or BS EN ISO 6940 and 6941
- Spanish, M Class or European Standards BS EN 13501: Class M1 or Euroclasses A1, A2 or B
Fixtures
- It is strictly prohibited to make any fixtures to the hall installations, walls, floors, ceilings or columns
- All connection panels set in the hall floors must always be accessible
- The exhibition surface area may not be covered with either paint or glue. The only permitted covering for the exhibition space is a platform or carpeting which must be removed by the exhibitor at the end of the event including the removal of any adhesive tape
- Any damage incurred to the venue infrastructure or installation, by exhibitors, their contractors or visitors, will be repaired by Fira and charged to the exhibitor
Floor Covering
Floor covering is compulsory. Floor coverings must be secured and maintained so that they do not cause a hazard. Exhibitors must take adequate precautions to protect the venue floor from damage.
- Bolting, fixing, or screwing to the hall floor is prohibited
- Paint or plaster must not be used on the floor
- Only double-sided adhesive tape may be used to fix floor coverings, which must be removed at the end of the Event
- All costs relating to damage or cleaning of the venue floor will be charged directly to the Exhibitor
- Fitted carpets, other textile floor coverings and under-lay must comply with British Standards BS 4790 Spanish or M Class or European Standards - BS EN 13501. Documentary evidence or labelling is required
- Mats shall be sunk, so they are flush with the floor of the stand
Floor Service Chests / Floor Ducts
All service chests must be accessible at all times. Platforms must have access to the service chest underneath. All stands with a platform higher than 50mm on which people could stand must have an access ramp, please click here for visuals. Please read the Ramps - Disabled Access section above for more information.
Platforms for electrical cables only should be at least 50mm, however if a water connection is planned for any neighbouring stand the a platform of 100mm if needed. Exhibitors who are planning to install a platform of less than 100mm should first check whether neighbouring stands would rely on a service check within their stand space for a water connection.
If a cable gets unplugged for any reason, the chest needs to be accessed by the technical teams.
Whenever a service chest is half covered by a division wall or is at the limit of the stand, the area around the chest must remain accessible.
Gangways / Aisles
- All gangways must always remain unobstructed and accessible
- Under no circumstances will any part of a stand, furniture, exhibits or displays be allowed to project beyond the boundary of your stand
- No doors, windows or any other element including lockers shall open outwards onto a gangway
- Night sheets must be tied securely and neatly throughout the day and avoid obstruction to gangways
- Building across gangways is not permitted
Glass / Glazing
Any uninterrupted, large areas of clear glazing or mirrors must be indicated with warning stripes, dots, logos, or other similar means. Corners must be polished or protected if they would otherwise pose a hazard to people striking them.
|
![]() |
Handrails
- A continuous handrail must be provided where there are two or more risers
- Handrails shall be non-climbable, i.e., with solid infills or vertical guardrails, which should be no more than 100mm apart and without horizontal members between verticals
- The height of a handrail shall be a minimum of 900mm measured vertically from the pitch line of the stair to the top of the handrail
- Handrails shall be continued as necessary around landings
- Handrails shall not project on to the required width of the staircase for more than 100mm
- All projecting ends of handrails shall be designed and constructed to avoid injury to persons descending a staircase
- When the upper level of a double deck stand has been built, it is mandatory to install railings (either temporary or the definitive railings) to prevent falls from height. The protection of railings needs to cover all of the area where there is the risk of falling
- In the case of glass walls (floor to ceiling) in the upper level of a double decker stand, where there is the risk of impact by an object, a railing or a similar physical barrier alongside these, needs to be set in place
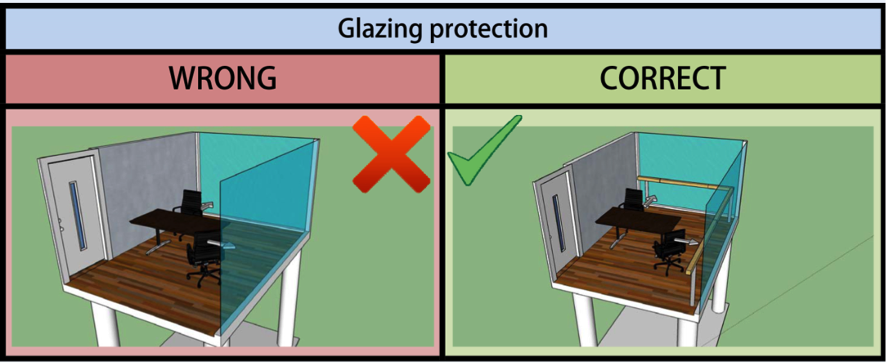
All kitchen spaces must adhere to the following:
- Floors and walls must be in good condition, without cracks and easy to clean
- Roofs must be provided over food preparation areas
- Sufficient lighting must be provided to allow work to be carried out in a safe manner
- A sink must be installed with drinkable water, equipped with antibacterial soap and paper towels
- All handling surfaces must be smooth, non-permeable and easy to clean
- Any areas being used to handle or store food must be designed to allow enough room to work and not located in walkways
- Food temperatures must be maintained as per the guidelines, hot food over 65ºC / 149ºF; cold food under 4ºC / 39ºF
- Office temperature should be a maximum of 25ºC / 77ºF
- Waste bins must have automatically activated lids with bin liners
Late Work
Contractors have the opportunity to apply for late working during build-up and dismantling.Please note:
- Only switchboards with 24h power will be in use during work outside of official hours. All daytime switchboards will be turned off at 22:00 as per the regulations. If you need a daytime switchboard to be working during late work please indicate this when ordering the service. Additional power can be provided (if technically possible) at the corresponding cost
- Contractors who have more than one stand in the same hall will only need to pay once
- Contractors who are building in different halls will need to pay once per hall
- On Sunday 2 March, late work is not permitted
- Construction work during the event open days is strictly prohibited. For security reasons such work is not permitted even outside the official opening hours
Lifting / Forklifts
Forklifts are permitted within the halls. These may be hired to help unloading and loading of your vehicle in the loading areas as well as movement inside the halls. Forklifts must be booked prior to the show with Resa Expo Logistic to ensure the required safety checks are carried out. For safety reasons you cannot use your own forklift on the venue premises. If you wish to dry hire a forklift, you may do so through the appointed lifting contractor, Resa Expo Logistic however please note that a qualified forklift licence will be required upon contracting. Under no circumstances is a dry hired forklift to be driven by any other driver onsite other than the driver who is qualified and provided their license upon signing the terms and conditions provided by Resa. Any person found to be driving a forklift who has not been granted permission will be removed from the venue.Luminescent Displays
The luminescence of projections, electronic lighting display walls such as LED walls or other types of luminescent displays or general lighting within stands may have to be adjusted to avoid disturbances to neighbour stands. Such devices should be placed in such way as not to affect surrounding stands.Material Handling Safety Precautions
Safety Equipment and Inspection:
- Emphasize safety measures during material handling: safety footwear, approved gloves, and safety helmets.
- Materials must be inspected for sharp edges, dirt, etc., before handling to determine optimal grip points.
Safety on Loading and Unloading:
- Stress slow, secure movements during loading and unloading; heavy or large materials should preferably be handled by two individuals or using mechanical aids for heavier loads (>25kg). Manual lifting between two people must be properly coordinated.
- Mandate the use of mechanical aids like forklifts or electric pallet trucks whenever feasible; compliance with load limits and braking system requirements is essential. Workers using this equipment must be adequately trained.
Organization and Safety Regulations:
- Trucks or vehicles must be fully stopped and use of handbrake is mandatory.
- Loads should always be secured against accidental movement. Nevertheless, maintain a safe distance from areas where materials might fall.
- Unsecure and arrange materials in accessible positions only when moving the load.
- Climbing on or over materials is strictly prohibited.
Fall Prevention Measures:
- Implement safety zones to prevent falls and regulate the presence of workers in potential material drop areas.
- Workers should stay at a safe distance around a mobile platform truck to avoid being struck. Only when the platform is on the ground level, workers should approach to access to the loads.
Stacking Heights and Secure Handling:
- Regulate stacking heights and methods to avoid exceeding recommended limits, ensuring proper stability of the stack.
- Properly instruct on the use of auxiliary elements like ladders during material transportation, emphasizing shared safe practices.
Safe Truck Loading and Material Placement Guidelines:
Importance of Load Placement: Risk Factors Due to Poor Placement
- Stress the significant impact of incorrectly placed loads, which can lead to severe accidents, material damage, and casualties.
- Highlight statistics indicating that 25-45% of road freight transport accidents result from improperly placed loads, underscoring the critical importance of this aspect in transportation safety.
Key Aspects to Consider During Load Placement: Preventing Loose Objects
- Emphasize the avoidance of transporting loose objects that could destabilize the vehicle, create distractions for the driver, or hinder driving due to noise or dust.
Load Distribution Factors: Centrifugal Force and Weight Distribution
- Explain the significance of uniform weight distribution to counteract centrifugal forces and ensure stability by lowering the truck's centre of gravity.
Friction and Blocking Force: Ensuring Load Stability
- Define the roles of friction and blocking forces in securing packages, highlighting the necessity of load securing accessories to enhance these forces.
Weight and Maximum Load Consideration: Attention to Load Weight and Vehicle Limits
- Emphasize the importance of considering package weight when loading and how it impacts the choice of securing accessories based on the vehicle's load limits.
General Recommendations for Load Securing:
Optimal Weight Distribution: Placing Heaviest Objects
- Advise placing the heaviest items at the base or on the floor of the truck to prevent potential damage or imbalance during sudden movements.
- Recommend positioning heavier packages closer to the axles for better balance and stability, avoiding placing them on the sides or top.
Utilization of Fastening Accessories: Importance of Load-Securing Tools
- Highlight the significance of using a variety of accessories (e.g., tie-downs, ratchets, load bars, straps, rails) to secure cargo and prevent gaps or movement between packages
The maximum floor loading capacity are as follows:
|
*Any other area: Information on request.
Click here to see the floor loading on a map.
Please click here to contact servifira for any further information.
IMPORTANT: Special conditions apply to double deck stands in Hall 8.1:
- Point loads can only support up to 6000kg
- The minimum distance between columns has to be 400cm
- Base plates of 50x50cm are compulsory on double decker stand columns
- Take into account the load limits and dimensions of the goods lifts in Hall 8. Click here for more information
Paint & Surface Treatments
- Only water-based paints or adhesives may be used on site. Protective measures must be taken to ensure that no paint or adhesive is spilt or sprayed on to the fabric of the building
- Fabrics and materials treated with fire resistant solutions should not be over painted with water-based paints
- For Spanish or M class or European classes, paints should be of class M0 or M1 (euroclass A1, A2 or B) and be supported by documentary evidence. Nitrocellulose based paints are prohibited
- The cladding has to be done by the Exhibitor’s stand builder in accordance the rules laid out in this manual
- The height of this type of cladding should not exceed the highest build element of the Exhibitor’s stand
- The cladding must be approved in accordance with our Stand Plan Submission rules
- It is not permitted to create extra space for storage, etc.
- Any service boxes must always be accessible
- If there is no agreement between the parties facing the pillar, the pillar must be left as is and might be clad in a neutral colour by the Organisers
- Where pillars are touching a stand boundary or they are located part on the gangway and part on one or more stands, the affected stands only have the right to clad the pillar and come to an agreement who can brand which side.
- The Organiser always the right to refuse proposals of cladding
- The front of the fire equipment needs to remain accessible
- When cladding around a fire hydrant that is equipped with a panic button, an opening on the cladding to access the button must be provided. The opening needs to be large enough for a hand to comfortably reach inside to hit the button (minimum 15x15cm). Signage needs to be provided close to the opening to facilitate its location and visibility
- The exhibitor may request fixed signs attached to pillars or walls to be removed if they collide with the stand structure. Only service personnel from the Venue are permitted to remove the signs, there will be a cost to the Exhibitor associated with this. It is the exhibitor’s responsibility to substitute this signage in the same place where it will be visible, at the same height or the closest possible to the original position
- The temporary signage needs to indicate the same elements as the signage removed
- The substitute signage needs to comply with the UNE 23034:1988 rule in terms of characteristics and size. The replacement sign must be the same size as or larger than the original
- It is also the exhibitor’s responsibility to provide temporary signage for these elements if their construction is obstructing the view of the existing signs
- Signs need to be auto luminescent in order to be visible in case of a power cut
- Check the fixed fire equipment signage specification for detailed information on pillar cladding, fire equipment and signage
The Organisers reserve the right to refuse any designs or request amendments to designs, which in their opinion have a detrimental effect to neighbouring exhibitors or the overall look of the exhibition.
Pin Spots / Stick Lights
- Pin spots cannot be fitted below 2.5m height measured from the hall floor
- At 2.5m or above, stick lights up to 300mm length are allowed
- Only stands 6m in height are allowed stick lights up to 500mm in length
- No other forms of lighting overhanging the gangways are permitted
- All lighting must be shown on stand drawings
- Any stick lights found on site without prior approval will have to be removed
Plastics Materials
- British Standards: Plastics must conform to the requirements of BS 476-Part-7-Class 1 Fire Regulation. Plastic plants, trees, etc. must also conform to this standard. Polycarbonate materials such as Lexan and Macrolon are acceptable. Perspex must not be used
- Spanish or M Class: Plastic must conform to the requirements of M0 or M1. Documentary evidence is required. Plastic plants, trees, floating decorations etc. must also conform to this standard. Perspex must not be used
- European Standards BS EN 13501: For M0 class above read A1 or A2. For M1 class above read A1, A2 or B classes. Documentary evidence is required
Platforms
Platform edges must be fully highlighted. The use of the platform must be included within the risk assessment. Platforms and ramps can be ordered from servifira.
Plumbing
- There are water and drainage outlets in the Halls, if additional conduits need to be installed, these will be charged to the Exhibitor. The screw-thread is 1/2" and the drainage channel is 32mm
- Pressure piping with double sided threads should be used for piping
- Water pressure in the Venue piping system is four (4) bars. At night this can reach five (5) bars
- For apparatus that require a constant water pressure, it is recommended that regulators are used and, where necessary, devices that increase the pressure
- The Organiser takes no responsibility for interruptions or irregularities in the water supply
- Without exception the basic regulations governing internal installations to supply water must be complied with
Ramps – Disabled Access
All stands with a platform higher than 5cm on which people could stand must have an access ramp. The slope of any ramp shall be uniform and no steeper than 1:10. Level landings shall be provided at the top and bottom of ramps and any intermediate position where exit doors open on to them. The minimum width of the ramp should be 1m. This slope should be within the stand and should not protrude into the aisle.The below table shows a summary of the rigging restrictions and pre-rigging areas. Exhibitors must check with the official rigging supplier in all circumstances.
Hall |
Build Height Restriction |
Exceptions |
Rigging restrictions / Pre-rigging areas |
Hall 8.0 |
5m |
There are some restrictions in this hall, please view the floorplan for further information |
Click here to download the H8.0 floorplan |
Hall 8.1 |
5m |
n/a |
Click here to download the H8.1 floorplan |
- The minimum distance permitted between rigging points for hanging elements is 1 meter
- The allowed maximum hanging weight of rigging elements is 15 kg/m2 calculated by the ratio between the total weight of the suspended elements and the contracted stand surface
- It is not permitted to lift up one truss grid with more than 6 manual chain hoists
- Exhibitors planning to use an electrical D8 plus chain hoist are required to submit documentation
- The maximum load weight of a rigging point in halls 1, 2, 5, 7, 8.0 and 8.1 of the Gran Via venue is 150 kg (1.47 kN). Subject to a technical and structural feasibility study, high capacity rigging points (HCP) with a maximum weight of 250 kg (2.45 kN) can be installed in halls 1, 2, 5, 7 and 8.1. In all cases, the weight of the lift itself (motors, hoists, etc.) must be included.
All suspended structures are considered ‘complex structures’ requiring load distribution calculations and structural certification through the official stand plan inspection agencies, except:
- Lighting trusses (without cladding) that use less than 10 rigging points
- Aluminium and fabric light banners with a maximum weight of 100kg per rigging point (including weight of the lifting elements)
All rigged elements must be inspected onsite before being lifted (see further down this paragraph). For further details please seethe Stand Plan submission section below or contact the official rigging company directly. Any additional costs are the responsibility of the Exhibitor.
Rigging height restrictions for the stand space should always be checked first. These can be found in the rigging restriction floorplans in the Appendix of the Venue Rigging Regulations.
Fixing points will only be provided when requests fall within the allowed parameters of the stand space.
- A fully dimensioned drawing in .dwg format
- Weight loadings of each ordered rigging point, considering the load of points and distance between points
- The dimensions of structure to be hung
- All rigging and materials should be in accordance with the Rigging Guidelines and the material specifications. To download Rigging Guidelines please click here (updated regulation will be available soon)
- Hanging any element above the specified height limit. The Build Height Restrictions section of this manual must be observed
- Rigging orders must be placed by the deadline. Any required rigging will be subject to sufficient time being available to carry out the work
- All rigging on stands must be finished by the Saturday before the Event as machinery is not allowed to enter the hall and no work at height is permitted after that day
- Rigging is not permitted above turnkey packages or above public gangways
- All rigging must be installed by the official rigging supplier. All suspended fittings and apparatus (e.g., lights, TVs sound clusters and speakers, display rigs etc.) must be fitted with secondary safety wires/chains and brackets
- It is strictly prohibited to tamper with any equipment installed by the official rigging supplier, including trusses, cables, shackles or slings
- Exhibitors own truss structures are only permitted they bear the CE mark (European Conformity) and is in perfect working condition. Roof trusses in each hall have different load bearing characteristics. Exhibitors and their contractors are not permitted to suspend from trusses themselves
- All rigging requests will be reviewed by the official structural technicians, Graó Tècnic
Before lifting any rigged elements, Exhibitors or their contractors must advise Graó Tècnic, or contact the hall manager, to have the hanging connections inspected, otherwise additional costs for inspecting connections at height will be charged to the Exhibitor.
Rigging points are provided with a ring or a hook, modifying any part of these fittings is not allowed.
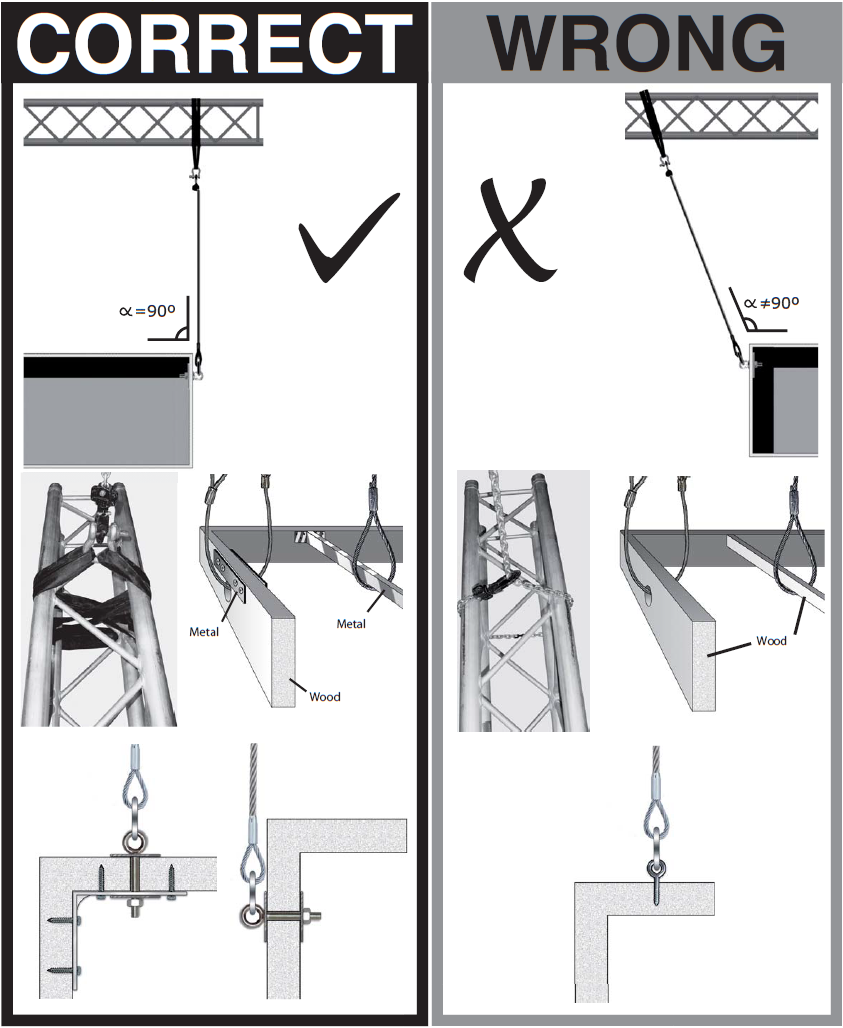
Orders may be taken after the deadline but will be subject to a late order surcharge.
In order to design rigging points adequately, Exhibitors and their contractors should consider the following advice:
- All rigging requirements MUST include scaled plans and weights to be checked
- The position of the stand should be referenced with the position of the neighbouring stands and/or aisles and doors
- The position of the rigging points should be shown with 0X,Y-coordinates, taking one of the corners of the stand as the origin of the coordinates (0,0). This can be achieved by using an Excel spreadsheet or by indicating it directly on the CAD drawing with dimension lines
- Vivid colours should be used for the rigging point symbol. A legend should be created to clearly identify rigging points on the plan. Indicate if it is a simple point, point with safety steel, manual chain hoist or electrical chain hoist
- Indicate the rigging point’s heights (O-ring), in a table with the reference of the rigging point number. This is compulsory in case the hoists are not provided by the official rigging supplier
- The distance between the rigging points for lighting / branding trusses should not be further than 10 meters apart
- Location of rigging points normally are at the end of trusses / crossings, but in case of heavy weights, they can be designed by load distribution criteria
- Indicate the load per rigging point on the same drawing. Do not forget to include the hoist and the truss weight and distance between points
- Attach as much detail as possible in your AutoCAD drawings such as trusses (with a simple silhouette or a coloured thick line), lighting, branding, AV or any other hung element. Indicate final heights measured from the floor in a rough elevation drawing
- Heights of elements must be measured from the ground of the hall, not from the stand platform
Scaffolding Tower Integration
Assembly Instructions
Preparation and Quality Check:
- Ensure compliance with manufacturer instructions for scaffolding tower assembly, utilizing high-quality, well-maintained components with appropriate markings (CE or equivalent).
- Mandate essential components: guardrails, complete gap-free platforms, suitable support base / brake wheels, internal access ladder, diagonal braces, and skirting where necessary.
Safety Measures During Usage
Safety Gear Requirements:
- Specific mandatory safety equipment: safety helmets, reflective vests, and safety boots.
- Access points should exclusively be through internal staircases; all access hatches on platforms must remain closed to prevent falls.
- Strictly prohibit using guardrails as support and emphasize adherence to the manufacturer's maximum load capacity.
- Placing materials on the scaffolding is prohibited.
Fall Protection Considerations
Addressing Lack of Perimeter Protection:
- Detail the use of fall protection equipment in instances where perimeter safety is not guaranteed, requiring attachment to approved anchor points on separate structural elements.
Material Standards:
- Insist on quality standards for wooden platforms and metal tubes, prohibiting their use if they exhibit knots, defects, rust or corrosion.
Staircases
- Any upper deck that has more than 25m of distance to a staircase or is over 200m2 in size must implement an additional staircase
- Stairs should be no less than 1m wide and have a handrail. They should have a handrail on both sides if they are wider
- Staircases over 2.40m width shall have an additional central handrail
- Flights and landings should be guarded at the sides when there is a drop of more than 360mm or there are two or more risers
- Flights should be minimum 280mm in depth. The height of steps should be minimum 130mm and maximum 185mm
- Flights of curved Staircases should measure minimum 280mm in depth measured at 500mm distance from their inner edge
- Open risers are not permitted
- Full structural calculations shall be submitted for review as part of the plan inspection process
- A safety controller must be present to control public access to the second floor
- Doors shall not swing across landings.
- All nosing (a rounded edge of a step / a metal shield for such an edge) must be made apparent by means of a permanently contracting material 55mm wide on both the tread and the riser
- Purpose-built access to trailers, boats, caravans and other, similar exhibits must be risk assessed where they do not comply with the above regulations. As a minimum, they must comply with the following:
- The headroom must be a minimum of 2m
- The width may not be less than 450mm and must be at least equal to the width of the entrance to the exhibit
- The risers must not exceed 180mm in height (open risers not permitted)
- The Spanish build regulations CTE should be consulted for more detail. Please click here to view the Spanish CTE (Código Técnico de la Edificación)
Stand Partitions
Where there is no neighbouring stand adjoining the back-wall, as a result of neighbouring stand movements with little notice or other similar reason, exhibitor must finish all of the back wall down to the ground and may be, at the discretion of the Organiser, permitted to apply branding.
For all Space Only stands being categorized as Seating Area space, please note that no walling will be permitted in the area and only seating style construction will be allowed here.
- TECHNICAL REQUIREMENTS:
- The fuel tanks of motor vehicles must contain only sufficient fuel to move the vehicle in and out of the hall.
- The fuel tanks on all other petrol engine equipment must be empty
- The fuel tank must be sealed, wherever possible with a lockable cap
- All vehicles must be provided with a drip tray and shall be positioned within the boundaries of the stand so that any protrusions, doors, tail lifts etc., do not infringe the stand perimeter
- The running of engines during the open period of an exhibition is strictly prohibited
- Filling or emptying of fuel tanks inside the hall is strictly prohibited at all times.
- Battery must be disconnected (this does not apply to new cars which have on-board computer systems)
- DELIVERY DATE: It is advisable to deliver any vehicles on the last day of build-up. There are more risks of damage if the vehicle is positioned before this date
- COLLECTION DATE: Collection of the vehicle should be ideally on the final show day between 16:00 and 18:00 when dismantling is starting and before gangways become blocked up with storage items
- BUILD-UP PROCEDURE: All stand vehicles will have to go via the marshalling yard ‘Sot del Migdia’ and will not gain access if they go directly to the venue. Read more here.
- Fira Barcelona and the organisers do not take responsibility for any damages to the vehicle or any other items or stand constructions during move-in or removal of the vehicle
Strobe / Fast Changing Lights
All exhibitors / contractors wishing to use strobes or fast changing visuals on their stand are to notify the organisers 70 days prior to the start of the Event, with a clear, detailed explanation.The below regulations are mandatory when using strobes or fast changing visuals:
- Strobes are to be mounted as high above head height as is practicable
- The number of flashes or image changes is less than 5 per second (5Hz)
- Strobes are not permitted to be on, for more than 30 seconds at any one time
- Any effect should be positioned outside the normal eyeline of the public or delegates
- Where more than one strobe light is being used the flashes should be synchronized
- Warning signs must be present.
- Where possible, the lights should be bounced off walls and ceilings or diffused by other means so that glare is reduced.
- Continuous operation of strobe lighting for long periods over 30 minutes, should be avoided.
- Strobe lighting is prohibited on the staircases of all double deck / 2 storey stands
- The maximum intensity level allowed for this type of light will be 3000 lux measured at 2 meters from any point on the ground
- Any special effects on the stand should be positioned in a way that any neighbouring stands are not affected. Any complaints from neighbouring stands will result in the onsite Health & Safety representative investigating
- Under no circumstances may light be projected directly or indirectly on passage areas such as walkways, skywalks, aisle or common areas
Timber Treatments
Timber materials must comply with the following standards:
British Standards
- Timber used in construction and displays under 25mm thick must be impregnated to Class 1 standard, in accordance with BS 476 - Part 7. The exception to this is MDF, which is acceptable for use due to its density
- Note: Treated boards will have BS 476 - Part 7 - Class 1 marked on them
Spanish or M Class
- Laminated wood more than 18mm thick or non-laminated between 5mm and 18mm shall be labelled or certified to M3. Non-laminated wood more than 18mm should be assumed to comply with M3 without the need for supporting documentary evidence
- Wood-based composite or plywood below 5mm requires to be M1 supported by reports. It may also be impregnated with suitable fire proofing substances applied by an approved method to M2 standards if certificates are supplied with the name of the product, a description and date of the approved applications
European Standards BS EN 13501
- For M1 class above read A1, A2 or B classes. For M2 read A1, A2, B or C. For M3 read A1, A2, B, C or D. Documentary evidence is required and should be submitted along with your plans
Upper Deck Capacity
a. The official supplier, Servifira: our official and recommended waste management supplier.b. An external (non-official) supplier of their choosing: Exhibitors and contractors may choose a non-official waste management supplier of their preference.c. Self-Removal: Exhibitors and contractors can handle waste removal themselves.
Please note: Exhibitors and Contractors choosing self-removal must hire a minimum number of waste containers from Servifira to account for any debris left at the end. The quantity of containers required is based on the size of the stand.
Important Guidelines:
a. Sharp items must be properly wrapped and disposed of safely.b. All carpet tape must be removed from the floor to prevent damage.
a. Waste containers can be ordered from servifira, our official supplier, or hired through an external supplier.b. Waste containers can only be placed in a pre-assigned slot that will be allocated by Fira Barcelona.c. Only one container can be used at a time. Any exceptions must be authorised by Fira Barcelona in advance.d. Note for External Suppliers:
Operating inside the venue incurs a logistics fee for external suppliers.External suppliers will need to purchase a special vehicle pass to access the venue at the Logistics Office (Resa).External supplier waste containers are not permitted to remain in the venue overnight during the event period. They must be removed before the end of each day.
e. For more information, please contact Fira Barcelona at mwcbarcelona.waste@firabarcelona.com.
a. Before leaving the venue at the end of build-up and dismantling, every exhibitor/contractor must have their space inspected by a representative from the Waste Patrol Team.b. The Waste Patrol Team will issue a Waste Removal Handover Certificate as proof of a clean stand.c. Exhibitors without a Waste Removal Certificate may be subject to additional charges.d. To contact the Waste Patrol Team, please reach out to the respective Hall Managers.
Waste Penalties:
a. A 'clean-up' fee of €300/m2 based on the stand size will be charged to exhibitors for any materials remaining at the stand after the dismantling period. This fee is applicable regardless of the quantity of material left behind.b. Exhibitors will be charged a 'waste abandonment fee' of €5,000, in addition to the cost of removing abandoned materials within the venue.c. Please note that CCTV surveillance is in operation within the venue to ensure compliance.
Water
Water connections may be available for your stand or hospitality suite depending on where it is located. If your stand is located in Hall 2 or on the exterior, you must contact servifira in order to check that this service is available as there are limitations in these areas. Please click here to contact servifira.Stand Build Safety
FIRE SAFETY |
GENERAL HEALTH & SAFETY RULES |
FIRE SAFETY
Hot Work & Naked Flames
Hot work is any process that can be a source of ignition when flammable material is present or can be a fire hazard regardless of the presence of flammable material in the workplace. Common hot work processes are any work involving oxyacetylene cutting/welding, gas/oil blowlamps, grinders, tar boilers, LPG burners, soldering. When flammable materials are present, processes such as grinding and drilling become hot work, processes which requires a hot work permit issued by the Venue prior to the commencement of work.
- Exhibitors and their contractors are to indicate any hot work taking place on the stand
- Hot work must be carried out on concrete or on ground protected by heat resistant material at the cost of the Hirer
- All safety measures should be provided to ensure that persons are exposed to any danger or risks from the hot work Fire extinguishers are be provided and readily available for use for this area. Exhibitors must abide by any other recommendations made by the Venue, the Organisers and the Fire Safety authorities
- The immediate area must be clear of other persons and vehicles. No other persons or vehicles should be able to pass under hot works
- The immediate area must be clear of any combustible items
- The operative and others must be suitably protected from risk of burns and damage to eyes
- A suitable fire extinguisher must be provided close to the location of hot works
- A second operative is required to monitor the operation, to keep other people clear, watch for signs of a fire, and use the fire extinguisher if necessary
The hall manager should be contacted for further assistance.
Flammables: gas bottles, helium balloons, bioethanol, burners
Domestic Butane or Propane gas bottles, helium filled balloons or bio ethanol burners are not permitted inside the venue at any time.
Exhibitors requiring outdoor heating solutions, should contact servifira for further details. Please click here to contact servifira.
Fire Extinguishers
Fire Exits & Escape Routes
- Exit door lighting, fire signage and safety equipment signs must not be obstructed unless permission has been given by the Organiser and alternative arrangements made
- Stands must be set out in such a way that they do not interfere with access to any firefighting devices
- If firefighting devices are located inside the stand perimeter, they must always remain visible and accessible
- It is strictly forbidden to custom build cupboards or doors in front of venue firefighting equipment such as fire alarm buttons, fire hoses or fire extinguishers
- It is possible to build cupboards or doors in front of firefighting equipment with the following conditions:
- Fire hoses, fire extinguishers and alarm button must be easily accessible. Note that fire hoses are provided with a glass door that must be easily open and hose must be pull out of its cabinet
- Fire hoses, fire extinguishers and alarm buttons must be properly signposted with normalized signs
- Door must be easily open without any lock
- Please note, these regulations apply for all periods, build-up, event days and dismantling
Capacity of exits
- The number, capacity and distribution of exits must be sufficient to allow visitors safe access and egress to ensure effective means of escape in the event of an emergency
- The exits must always be kept available and unobstructed and should generally be arranged so that there are alternative escape routes from any point within the event
- The capacity of exits is subject to the specifications under Spanish build regulations CTE (Código Técnico de la Edificación). Please click here to view the Spanish CTE (Código Técnico de la Edificación)
All Emergency Exit Doors must comply with the following:
- Doors must be non-lockable, for example with a anti panic push bar
- Doors must have a system of easy and fast opening accessibility, on the side from which an evacuation would occur
- Doors must open in the direction of the evacuation
- Doors cannot invade hall aisles
Stands over 150m2 require minimum two emergency exits on opposite sides of the stand on the ground level.
Escape routes within a stand perimeter must comply with the following lengths and widths:
- Stands up to 100m2 1m width minimum
- Stands over 100m2 1.5m width minimum
- The maximum length of an escape route on a stand is 15m until an open area is reached
- Should the escape route be longer than 15m a 2m width minimum or an alternative escape route must be created, leading to the opposite side of the stand
- If the above cannot be achieved due to the large size of the stand, the stand should be designed in such way to ensure the shortest possible escape route. All layouts must be checked individually by the stand plan inspection agencies and are subject to onsite inspection. Please read through the Stand Plan Submission section below for further information
Spanish regulations state that all signs must always be visible even when there is a blackout.
Please read through the Stand Plan Submission section for stands over 500m2.
Fire resistance of load-bearing elements of double deck structures
Two Storey / double deck structures larger than 500m2 must provide evacuation calculations for the first floor following the Spanish building regulations (CTE). Please click here to view the Spanish CTE (Código Técnico de la Edificación)
If evacuation time is less than 2.5min (25m is considered less than 2.5min evacuation time):
- The structure around emergency staircases (pillars and buttress) must be treated for fire resistance. R-30
- 50kg fire extinguishers must be provided on the evacuation route near stairs on second deck
- Emergency and evacuation assistants must be placed in each emergency staircase
If evacuation time is more than 2.5min there are two options:
- The entire structure of the upper level must be treated for fire resistance, or
- The number of emergency staircases is increased until evacuation time is reduced to be below 2.5min. Subsequently, the above rules apply for evacuation times less than 2.5min
Material Specifications
Please refer to the Fabric & Decorative Coverings / Materials section above, for details of which materials can be used and how they are classified. Flammable materials may not be used for the construction or assembly of stands. The materials employed shall not contribute to the evolution of large volumes of smoke.
All materials used must meet the relevant Spanish build regulations (CTE), British, M or Euroclass standard. Please click here to view the Spanish CTE (Código Técnico de la Edificación).
Smoke Detectors
General
- Ceiling structures are permitted providing the material specifications laid out this manual are followed. Test certificates should meet DIN 4102-B1 or its equivalent standards. Relevant certificates must be available for presentation upon request
- Stands with enclosed ceilings, measuring up to 6m in height that do not allow the release of smoke, must have smoke detectors and a fire alarm system to CE certification, fitted
- A minimum of one smoke detector for each 60m2 of enclosed ceiling is required, i.e., an enclosed ceiling of 100m2 requires minimum of two smoke detectors
- In narrow aisles and covered spaces less than 3m wide, the minimum distance between detectors must be 15m
- For stands with less than 100m2 enclosed space, independent, autonomous smoke detectors with integrated alarms are acceptable if they are certified CE norm
Please note: Conventional textile ceilings are classed as solid ceilings and will require smoke detectors.
General Exceptions- If the ceiling area to be covered is less than 40m2, the correspondent smoke detector can be avoided if the covered ceiling has at least two openings of 300mm x 300mm, on opposite corners of the room to be covered
- Ceilings made from textile wire mesh are accepted without a smoke detector if they are fire resistant M0, M1 or M2 (Euroclass A, B or C) and have a minimum opening of 2mm x 4mm or 3mm x 3mm. Textile ceilings are to be one layer only and stretched horizontally
- Ceilings made with a metal grid are accepted without a smoke detector, if they are fire resistant M0, M1 or M2 (Euroclass A, B or C) and have a minimum opening of 10mm x 10mm
- Stands with enclosed rooms under a second level (regardless of the m2) or with more than 100m2 enclosed space will require the following:
- A professional smoke detector system that meets the requirements of UNE 23007-14:2009 including
- Alarm buttons
- Interconnected smoke detectors
- Control panel
- Certified by an authorised and competent local supplier
- At least one smoke detector per enclosed room
- The smoke detector system must be connected with the Venue Control Centre using a communication device which must be hired from servifira
- The smoke detector system requires a 24h power supply in order to operate correctly
Exhibitors are advised to contact servifira for a quote regarding installation by the venue official supplier of these systems. Below is an example list of some requirements for such installations:
- Alarm buttons must be placed so that any person within these spaces should not have to move more than 25m in order to reach/press the alarm button. In places where it is expected that users may have limited mobility, the distance covered should be reduced. In general, the buttons should be set at a height between 1.2m and 1.6m from the floor
- The sound of the fire alarm must have a minimum level of 65 dB (A) or 5 dB (A) above any other noise that will probably persist for a period of 30 seconds if this level is higher. The sound level should not exceed 120 dB (A) at any point where there is likely to be people
- Please click here to see a diagram of how such smoke alarm systems should be installed
IMPORTANT:
In the event of an alarm on the stand, the exhibitor is fully responsible in the first instance to investigate the reason for the alarm as well as notifying the Hall Manager or H&S Team onsite. It is in the best interest of the exhibitor to allow the venue and Westpoint on to the stand as soon as possible to check the alarm. Failure to do so can delay any action required, the length of time the alarm sounds, disturbing visitors and neighbouring stands as well as the possible health & safety risk.
Exhibitors planning to install a kitchen as part of their stand design must include a detailed layout indicating the exact location of any electrical equipment (ovens/kettles etc.) on the stand plan submission, allow for this to be checked as part of the plan inspection process.
Exhibitors wishing to contract a smoke detector installation should contact servifira for further information. Please click here to contact servifira.
GENERAL HEALTH & SAFETY
- The installation of electrical power onto stands and other temporary structures and facilities, must be undertaken by the venue appointed electrical contractor. The nominated contractor will liaise with the exhibitor or contractor to ensure that the installation is verified as safe prior to it being connected
- Details of the power supply available at the venue and the detailed requirements for each stand type are listed in the power supply section of this event manual. This information includes the voltages and the number of socket outlets which will normally be provided. The venue and stands power supplies will be protected by 30mA residual current and over current protection. In these circumstances, should the supply be overloaded or have dangerously faulty equipment, the local circuit breakers will cut the power to the stand automatically
- Exhibitors requiring a larger power supply may arrange this with the venue at an additional cost, up to a maximum rating as specified in the Electrical Rules. Because of the obvious fire and electrical danger, the rating of the supply must not be exceeded
- Contractors working at the venue must ensure that all power tools in use are suitable for use with the local supply
- Exhibitors and contractors are required to provide their own extension leads or adaptors and are responsible for them being properly wired and electrically tested. All electrical equipment and extension leads used must have been subject to combined inspection and test by a qualified electrician, including insulation and earth bonding tests, and must not be overloaded
- ‘Daisy Chaining’, the joining together of two or more multi-way extensions or plug-in adaptors, is strictly not allowed. This practice overloads circuits and can be a source of fire. Any ‘daisy chained’ units will be disconnected; removed and electrical power to the stand will be disconnected until the electrical contractor is satisfied that the installation is safe. The use of a multi-way plug-in adaptors and extension leads is restricted to one unit per fixed socket outlet
- Inspected equipment must be clearly labelled with inspection labels and a certificate of inspection must be available on the stand
- Any electrical equipment on the stand must be in good condition with live conductors enclosed and inaccessible, and cables properly protected against damage. Where an electrical installation is being wired or installed on site by the exhibitor, such work must be undertaken by a qualified electrician in accordance with the electrical safety rules and local wiring codes. As detailed in the rules, the electrical installation of each stand will have to be tested and certified before the stand is energised and will be disconnected if it is not properly installed and safe
- Any portable handheld electrical equipment used outdoors by contractors must be of double insulated standard and supplied from a circuit protected by a 30mA RCD
- Exhibitors and contractors are not permitted to carry out work on the venue’s electrical installation without written permission by the venue
- Electrical supplies to the stands must be isolated prior to dismantling
- The Organiser, the venue and their agents reserve the right to remove or disconnect any electrical equipment which either appears defective or has inadequate evidence of electrical inspection
- Exhibitors and contractors are advised follow the current Regulation of Low Voltage (Reglamento Electrotécnico de Baja Tensión) published in the Royal Decree 842/2002 (Real Decreto 842/2002). Only Spanish regulation will be accepted
- All clients' own fittings including displays and light boxes must be complete with all connectors fully enclosed and having an earth connection at every fitting
- Flexible leads for static appliances must not exceed 2m
- Stand switch-fuses must be always accessible
- Appliances must have been tested by competent persons before energising. The person bringing the equipment into the hall is responsible for the test being carried out
- Bare conductor catenary low voltage systems are not permitted
- Electrical installations that do not comply with the Regulations will not be energised
- The Organiser reserves the right to disconnect the electrical supply to any installation that in its opinion, the opinion of the electrical contractor or the venue, is dangerous or likely to cause annoyance to visitors or other exhibitors

- Isolation levels:
- Power supply main cable - The type of cable used in this segment shall be 0,6/1 kV isolation type
- Stand Installation - Conductors to be used in the stand installation must be 0.6/1kV isolation level
- Conductors of 450/750 V isolation level can be used with a rubber isolation (Type H07RN-F). For other isolations, please check tables 1 and 2 in electrical rules
- Colour code to identify the phase conductors is: black, brown or grey. Blue is identified for neutral conductor and the green / yellow for ground conductor
- Minimum section of the conductors depending on the protection installed
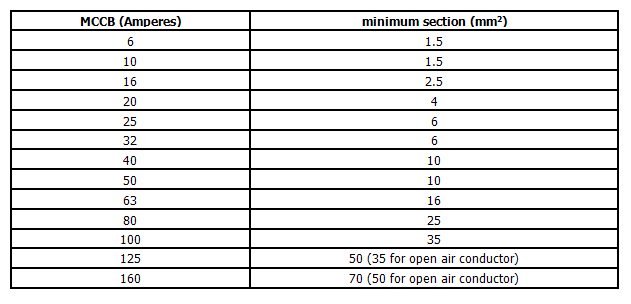
- The ground conductor must be of the same section as the phase – neutral conductors until 16 mm2. From 16 mm2 on, it can be reduced by half
- Metal structures, receptors and, in general, everything that has metal parts and that could become live if a fault occurred, shall be connected to the ground distribution
- All lighting circuits and outlets of less than 32A shall be protected with 30 mA residual current circuit breaker (RCCB). All electrical equipment that is accessible to the public must be also protected with 30 mA RCCB
- All circuits must be protected against overcurrents with omnipolar cut off (phase-neutral) in its origin
- The venue has the following electrical specifications:
- Working voltages: 230 V single-phase, 400X three-phase
- Frequency: 50Hz
- Maximum single-phase supply: 6.6 kW (32A). Electrical connections with a power greater than 6kW must be carried out the form of three-phase installations
- Power factor for calculation: 0.85
- Each service chest contains: communications, electricity, data, water supply and waste, TV and FM. The technical details of each chest are as follows:
- III 400 V (CEE plug)
- From 16 to 63amp supply
- 2 Connections of compressed air per service chest, 1000 l/ min. 6.5 bar
- 2 water supply connections per chest, half an inch, 4 bar, 32mm drainpipe
Personal Protective Equipment (PPE)
Important: All exhibitors and contractors in the halls during build-up and dismantling must wear appropriate Personal Protective Equipment (PPE) |
Exhibitors are responsible for ensuring that the appropriate PPE is always worn by all personnel working for or on behalf of the exhibitor. Exhibitors must ensure that all personnel working for or on behalf of the exhibitor, always cooperate with the organiser and the organiser’s appointed safety staff regarding health and safety.
- Safety helmets must be in accordance with UNE-EN 397. A chin strap is required when working at height
- High visibility vests must be in accordance with UNE 471. High visibility vests must be ‘day glow’, dark colours are not permitted
Other PPE
Flat shoes, pumps, heels of any kind (including trainer heels), wedges and open toed shoes such as sandals and flip-flops – are NOT permitted during build up and dismantling. |
![]() |
Religious Exemptions
Spain does not provide a religious exemption to the UNE-EN 397 safety helmet regulation. An individual may choose to wear a patka under the standard safety helmet.The Organisers will permit turban/dastaar-wearing Sikhs to enter the venue during build-up and dismantling without the standard safety helmet only if:
- The organisation requesting the individual’s entry provides their identification information so on-site staff may identify them
- The individual’s employer* notifies the Organiser at least seven (7) days prior to build-up, in writing, that the employer has permitted this particular employee a religious accommodation, including information on the way in which the proposed accommodation meets the requirements of UNE-EN 397
- The employee brings an alternative head covering which meets the requirements of UNE-EN 397, as pre-approved by the Organiser in its sole discretion, to wear onsite
Only the individual’s employer may permit the accommodation or request it from the Organisers.
Working at Height
A person is working ‘at height’ if there is a possibility of their being injured from falling, even if they are working at or below ground level. Generally, this means above 2m.All reasonable steps should be taken to eliminate or minimise work at height. Working at height should be properly planned and supervised and the correct equipment selected. The following guidelines must also be followed:
- Always consider measures that protect everyone who is at risk (collective protection) before measures that protect only the individual (personal protection).
- Collective protection is equipment that does not require the person working at height to act to be effective, for example a temporary guard rail or a net.
- Personal protection is equipment that requires the individual to act to be effective. An example is putting on a safety harness correctly and connecting it, via an energy-absorbing lanyard, to a suitable anchor point
- No work is to be performed at height if it is safe and practical to avoid it
- All work at height must take account of conditions that could endanger safety, such as high winds or slippery ground
- Those working at height must be protected by a guardrail or be equipped with a fall arrest harness (except when using a ladder)
- Those involved in work at height must be trained and competent
- Equipment for work at height is appropriately inspected and free from safety defects
- The risks from falling objects are properly controlled. Work platforms must have a toe board to prevent items falling
- Access is controlled to prevent other persons working or walking beneath work at height
- Persons working in the vicinity of high works must where a safety helmet
- Persons working at height on mobile elevated work platforms should wear a safety helmet with a chin strap
- Plans are in place for emergencies and rescue from height
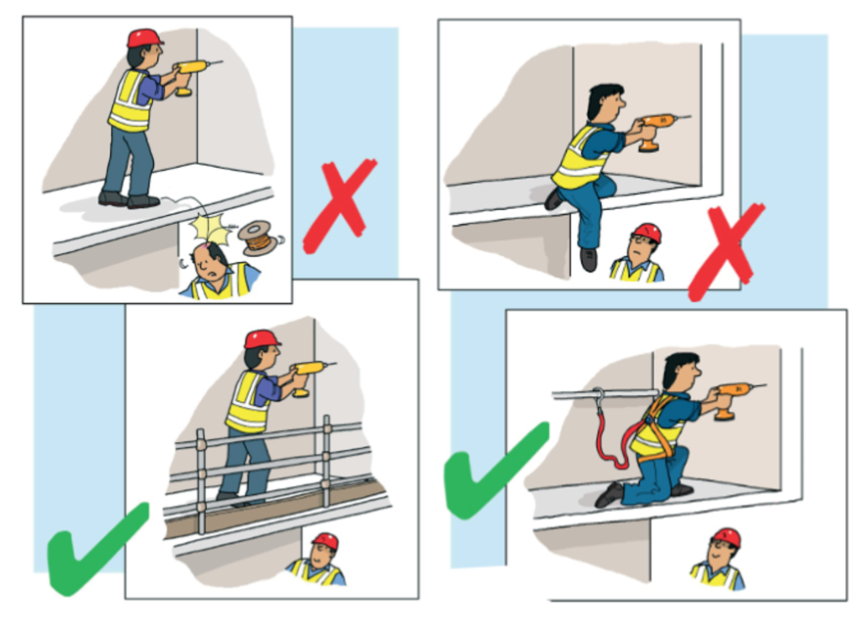
Further guidance on how to plan safe working at height can be found at the following links.
- Planning for working at height
- Stop the Drop_Flowchart
- Ladders
- Mobile Elevating Work Platform
- Mobile Scaffolding
Exhibitors building a Double Decker stand must plan for preventive safety measures for any work at height. Not doing so may result in substantial delays or closure of the stand.
Important: Working close to an unprotected edge will not be tolerated. Free-walking on any structure is prohibited. All work conducted at height must be properly risk-assessed and suitable Personal Protective Equipment must be used. Upper levels must be properly guarded and, where assessed as appropriate, fall-arrest PPE used continuously. |
- Provide the most suitable equipment appropriate for the work
- Ensure all the equipment complies with the European regulation
- Always follow the manufacturer’s instructions for work equipment
- Only use equipment on firm level ground
- Ensure equipment for work at height is appropriately inspected
- The risk of falling objects is properly controlled
Important: The Organiser reserves the right to require defective equipment to be removed from the halls. |
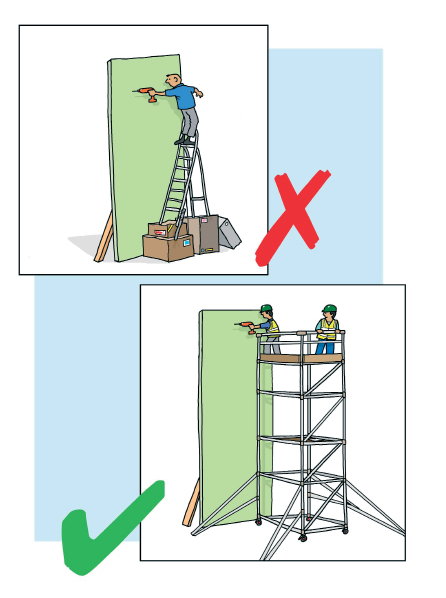
Additionally, the following guidelines must be followed:
- The use of portable ladders measuring 5m or more is strictly prohibited
- Ladders cannot be used for works over 4m. Scaffold Towers must be used in this case
- Ladders must have ‘industrial’ rating (this type are more durable and resilient)
- Leaning ladders must be placed at the correct angle
- Ladders should only be used on level ground and must be secure e.g., suitably tied or, as a last resort footed
- The top treads or steps must not be used as a platform for work
- Users should always face the ladder whilst climbing or dismounting
- Stepladders should not be used sideways-on where sideways loads are applied
- Only one person should climb or work from a ladder or a stepladder
- Steps and ladders should be checked for suitability and defects each time they are used
- All workers must wear a helmet to secure their safety
Important: The use of portable ladders five metres or higher are prohibited. Any ladder of this kind will be removed. Repeated noncompliance with this regulation will result in construction activity being stopped a period of time. |
Before erecting the tower:
- Check all the components are in good condition
- Check wheels for effective rotation
- Check brakes and locking devices work correctly
- Before erecting a tower on a suspended floor, ensure the bearing capacity of the floor is sufficient for the planned load
Before use:
- Ensure the tower is vertical and square
- Towers must not be used unless the wheels are locked
- Check that outriggers are set correctly and secured
- Ensure the platform is fully boarded out and that guard-rails and toe-boards are fitted if the working platform is over two metres high
- The gap between toe-boards and mid guard-rails and between mid and top guard-rails must not exceed 470mm
Stability:
- Never climb up the outside of a tower – use the stairway or ladder on the inside
- Follow the manufacturer’s instructions on base to height ratio
- Hoist materials up from the inside of the tower
- Do not move the tower if people or materials are still on the platform
- Do not pull the tower along while standing on it
- Towers must only be used on firm flat surfaces
Work Machinery & Woodcutting
- Operatives must be competent to operate the equipment in use
- Operatives must wear suitable Personal Protective Equipment (PPE)
- Work equipment used in build-up and dismantling must bear the CE mark and be in a perfect working order
- Powered tools must not be left unattended whilst operating or connected to the power supply. All dangerous parts such as saw blades must be guarded
- Protective devices must be used in the cutting areas and mobile elements
Important: All tools must be in good working condition and safe to use. The Organiser reserves the right to prevent the use of any equipment which is unsafe. |
- Please ensure all relevant machinery that generates dust is used with a dust bag. All contractors operating machinery without a dust bag will receive a warning. Repeated noncompliance with this regulation will result in construction activity being stopped a period of time
- Under no circumstances shall such machinery be used inside the halls within 48 hours of opening
Workplace Housekeeping
- Work areas are maintained in a neat and tidy fashion, to ensure a safe work environment
- Halls and floors are kept free of slip and trip hazards
- Waste materials are removed daily - contact servifira to purchase waste products
- Tools, equipment and materials are stored accordingly
- Gangways and fire exits are always kept clear
From Thursday before the show opens until the morning of show open, gangway carpet will be laid throughout the halls.
During this time, contractors must ensure the following:
- All waste is removed at the end of each day
- Gangways be always kept clear. All materials, equipment and tools must be stored within the stand footprint.
- Please note that the Organiser will not be responsible for any material left in the gangways
Stand Plan Submission
Exhibitors are responsible for ensuring that their stand designers and contractors fully understand the requirements and regulations set forth in this Event Manual, and are following all applicable regulations and legal requirements.
The stand plan submission process also includes the submission of certain mandatory safety documents which collectively make up the ‘stand plan submission’. The full stand plan submission includes:
- Detailed plans and designs
- Safety Risk Assessment
- Method Statement
- Double Deck Health & Safety *
- Waste Removal Information
More information and guidance on the above-mentioned safety documents can be found in the ‘General Safety Regulations’ section of this Event Manual, and by clicking on the links above. Stands plans and Waste Removal Information must be submitted directly through the Abraxys Plan Upload Platform - see link below, all other safety documents can be found in the Forms & Deadlines sections of this Event Manual.
Submission of all mandatory safety documents is a conditional requirement for the exhibitor's contractors to enter the venue during build-up. Once all plans and documents have been received and approved, a ‘Permission to Build’ Certificate will be issued. The Digital Contractor Pass' for all workers associated with a stand will not be activated until the ‘Permission to Build’ Certificate has been issued. Workers without an ‘active’ Digital Contractor Pass will be automatically refused entry.
Details of how you should submit your stand plans and documents are explained below.
The deadline for ALL plans and documents to be submitted is Monday 24 November 2025. |
Submission Process
- Technical drawings at a scale of 1:50
- Event and venue details, together with stand and hall numbers
- Metric dimensions clearly marked
- Plan and elevation drawings, together with a visual
- Details of all materials used, together with all required certificates
- Electrical plan
- Evacuation plan showing all necessary smoke detectors, escape route signage and locations of fire extinguishers
- Full details of any rigging requirements or hung elements
- Height of all elements, together with measurement of the highest point
- Vision panels in all storage and meeting room doors
- Evidence that all storage / meeting room doors do not open out onto the aisle. Storage or meeting rooms situated away from the aisles must have doors that open outwards - not onto a gangway, only inside the stand space
- Fixing details for suspended or cantilevered sections of the stand using suspension wires
- Detailed explanation of floor coverings, together with all required certificates
- Platforms – height, materials and details of wheelchair access ramp dimensions
- Confirmation that all platforms have rounded corners and edging to stop carpet lifting away from the edge of any platform
- Details of any large equipment and how it will be fixed securely, including secondary fixings
- Details of how stands will be finished at the top
Photographs, hand drawn plans, faxed drawings or drawings from other events will not be accepted
Upon receipt of the detailed plans and designs, Abraxys Ltd will determine whether the structure is 'non-complex' or 'complex'. Complex structures will require additional review and approval from Graó Tècnic, the official venue engineers. Abraxys Ltd will pass such plans to Graó Tècnic who will then take on direct contact with the Exhibitor or their contractor. Abraxys Ltd will coordinate all approvals and will issue the 'commence to build’ letter once all approvals are received.
Complex Structures
- Double deck stands with under passes or staircases to any area.
- Suspended structures that require ten (10) or more rigging points or are classed as 'complex' by Abraxys Ltd
- Platforms and stages over 50cm in height and those including staircases
- All outdoor structures (due to their possible exposure to harsh weather conditions structures built in the outdoors need to withstand wind speeds of up to 100km/h)
- Where there is a raised area (e.g., seating area) above the general height of the floor or platform.
- Where machinery or other heavy element is displayed other than at ground level. An example might be a machine which is on a steel frame to be seen at eye level. Structural calculations would be required, together with other details
- Where there is any form of tiered or ‘grandstand’ style seating
- Stands bigger than 100sqm due to local regulation regarding escape routes
Rules relating to the build of a complex structures are rigorous. All construction is subject to the rules and regulations of the Spanish CTE (Código Técnico de la Edificación). Please click here to view the Spanish CTE (Código Técnico de la Edificación)
All complex structures and complex suspended structures / rigging must receive a formal certificate of stability from Graó Tècnic, the official venue engineers. This certificate has a related cost which will be communicated to the Exhibitor by servifira.
The above descriptions are a guide only and due to the nature of the regulations cannot be comprehensive. It is the decision of the venue, structural engineers and Abraxys Ltd as to whether the stand must be deemed complex. Their decision is guided by global exhibitions regulations and local law, it is final.
The Organisers, the venue or the official structural engineers reserve the right to request structural calculations and approvals at the expense of the exhibitor, pre-show or on-site, for any structure at the Event as necessary.
- Distribution plans of both levels of the construction (if not included with other documentation)
- Calculations of the main structure which must include:
- Full structural calculations of all build elements, considering the maximum floor loadings of the exhibition floors. To view floor loading capacities, please click here
- Details on the load transmission of pillars to the exhibition floor, of any upper decks
- Details on the maximum horizontal impact strength of any walling or handrail element (minimum 1kN per m)
- Outdoor structures only: Details of wind stability (minimum 0.52kN/m 2(100km/h wind) according to Spanish build regulations (CTE). Please click here to view the Spanish CTE (Código Técnico de la Edificación)
- Double deck structures only:
- Fire resistance of load bearing elements of double deck structures
- Double deck structures bigger than 500sqm must to provide evacuation calculations of first floor following the Spanish build regulations (CTE)
- Author of the calculations, title, date of drawing & full contact details